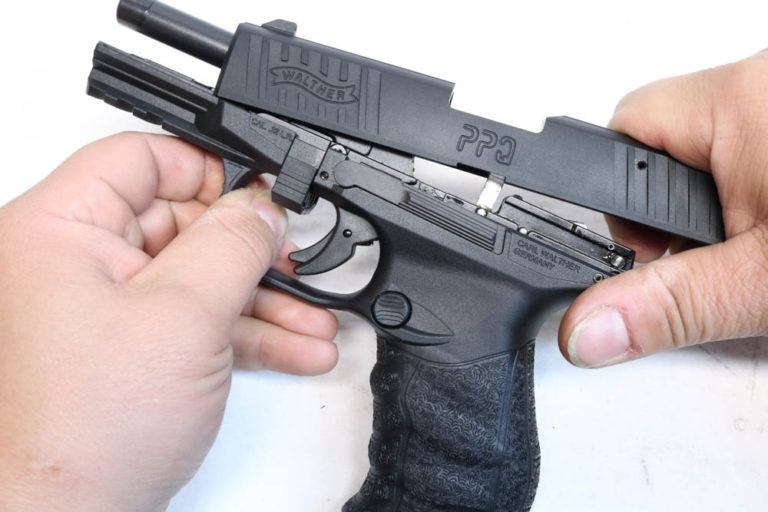
If you do your own gunsmithing long enough, you will run into screws that refuse to budge. From simple to extreme, try these five techniques to get the job done.
The five ways to remove frozen screws when gunsmithing are:
If you work on firearms long enough, you will run into screws that refuse to budge. With the correct screwdriver and the proper force, a screw should move. If it doesn’t, stop. Go through this checklist: Is the screw a properly fitting screw? When was the last time this screw was moved? Has Loctite been applied? If you don’t know, is it a screw that is likely to be locked in place? (The most common places you will run into screws locking in place will be on scope mounts. People who don’t know how to properly tighten a screw will use Loctite when it’s not needed.)
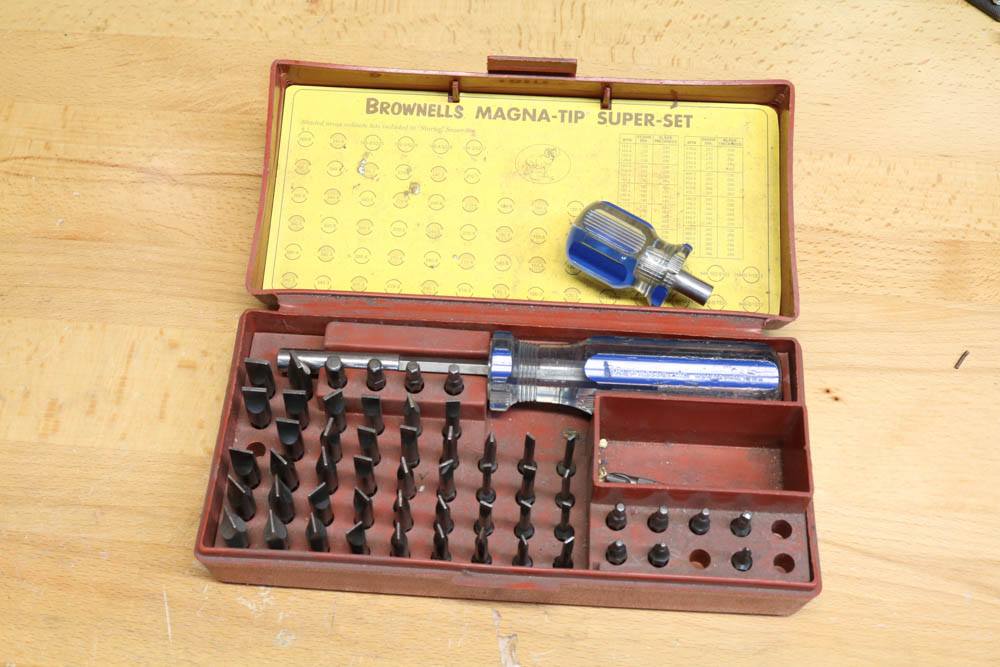
You must proceed with caution or you will mar or strip the screw slot, making a difficult job more difficult. Do not let anything slip. The screw or even the firearm will be damaged. In extreme cases, you can hurt yourself.
1. Use A Torch
Double-check you are using a properly fitting screwdriver. If the screw is locked in placed with Loctite, use a propane torch to break down the Loctite. You must be careful. The strongest grades of Loctite will withstand 400 degrees Fahrenheit. At 600 degrees you will heat-damage the bluing, but the steel itself will not be harmed.
2. Use Penetrating Oil
If the screw is frozen, but not locked in with Loctite, heat will have no effect. Put the firearm on your bench so the screw is level, and place a drop of penetrating oil, such as Liquid Wrench, on the screw head. Let the oil work into the screw for an hour, a day, or a week, if you can. Now try again with a screwdriver.
Some people prefer to work horizontally, others vertically. I’m a vertical person. I set the handgun on top of the padded vise, with the jaws open enough to let the frame fit in the droop of the padding. I hold the screwdriver vertically and place it into the slot. My chin rests against the end of the screwdriver’s handle while I use both hands to turn the screwdriver. In this way, I can exert maximum force and still feel for any movement of the screw.
A variation of this involves the drill press. Clamp the firearm to the drill press table. Put a driver bit that fits the screw in the drill press chuck. Make sure the drill press is not just turned off, but unplugged. Lower the drill press head, line the blade of the screwdriver up with the slot. Using a drill press to keep the screwdriver blade firmly in the screw slot, turn the drill chuck by hand. You can also, if there is room, get a wrench on he screwdriver shaft, for extra leverage. If the screw is completely immovable, or the screw slot has already been damaged enough that you cannot get the screwdriver to purchase, you must now resort to extreme measures.
3. Re-Cut The Screw Slot
Position a cutoff wheel in your Dremel tool. Grind the wheel down to a diameter small enough that you can re-cut the screw slot without touching the frame of the firearm or the base of the scope mount. This method works better with large screws.
4. Drill The Screw
Clamp the handgun in your drill press. DO NOT attempt this with a hand-held variable speed drill. If you simply attempt to drill, the drill will flex against the screw slot and “walk” to drill places you don’t want drilled. Clamp the handgun in your drill press. Use only a center drill. Drill the center of the screw down just far enough to drill off the head. You do not have to match the drill to the screw head diameter. So long as the drill is larger than the threaded portion of the screw, when you get down to the threads, the head will come off. This method is most useful when the firearm is plated, or the part being held by the screw is aluminum. You can now remove whatever the screw was holding on, and the screw shaft will turn out easily with a pair of pliers.
5. Welding
Take the firearm to your welder. (And for goodness sake, let him know you are coming, and why!) He can build up a post of weld on the screw, and then either weld a section of welding rod to the stub or weld a nut to the post. Either way, the screw will turn out, and it will be intact. The screw, having been welded on its head, can be turned, polished, and have a new slot cut. You won’t need to replace the screw. What you will need to do is repair anything damaged by the heat of the welding process. Any bluing or plating will be torched off around the screw. If the screw was holding down something made of aluminum, the torch would have destroyed it.
Editor’s Note: This article is an excerpt from Gunsmithing Pistols & Revolvers 4th Edition, available now at GunDigestStore.com.
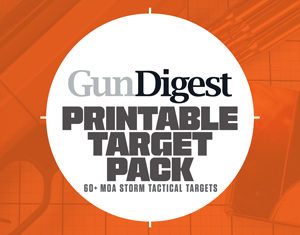
Next Step: Get your FREE Printable Target Pack
Enhance your shooting precision with our 62 MOA Targets, perfect for rifles and handguns. Crafted in collaboration with Storm Tactical for accuracy and versatility.
Subscribe to the Gun Digest email newsletter and get your downloadable target pack sent straight to your inbox. Stay updated with the latest firearms info in the industry.
I much prefer to use a heat gun rather than a torch. It will get plenty hot enough to soften the Loctite. No risk of damaging the blueing either. Kroil is great stuff and so is PB Blaster. These are the two best, in my opinion, much better than Liquid Wrench or any thing else I have tried. Have also had good luck using a small rachet that uses bits from Brownells and turning while someone else taps the top of the bit with a hammer.
A lot of heat guns go above 1000 degrees F, which would probably threaten your blueing. They also tend to cover a lot bigger area around a screw than a small torch tip does. Try a soldering gun with the tip touching the screw itself and nothing else.
Instead of liquid wrench I recommend a product called Kano Kroil Penetrating Oil. Called “the oil that creeps”.
This stuff is great! It can be found all over the internet, including at Amazon.