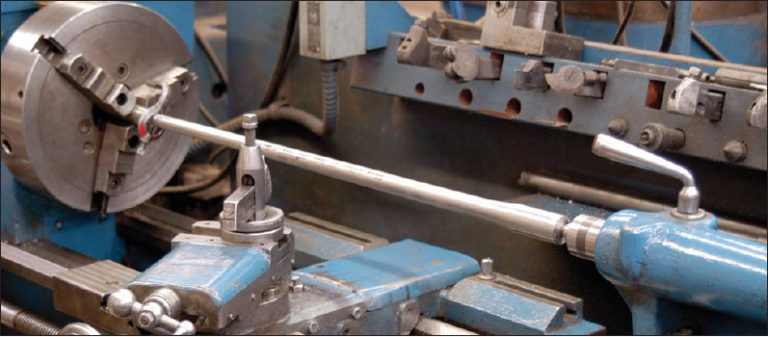
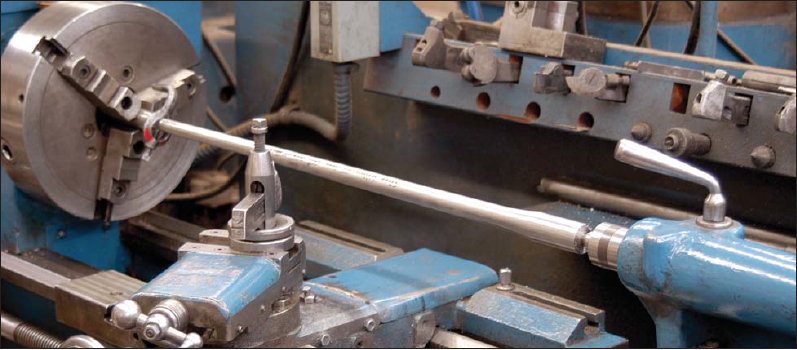
Learn about the three kinds of barrel rifling in this article about custom rifle barrels.
The vast majority of custom rifle makers do not manufacture their own barrels. It is simply too costly to perform this function in-house due to the cost of the equipment necessary and the relatively few barrels that the maker will require. This is, simply put, another area that required years of expertise to achieve anything close to perfection. Instead, they rely on specialists that usually do nothing but manufacture barrels.
The three basic methods in common use for rifling a barrel are cut, button and hammer forging. Each method is widely used for custom rifle barrels. Each can and does produce quality barrels.
Cut Rifling
Cut rifling is the oldest method and has been in use for about 500 years. I-read somewhere that it was invented in Germany about the time Columbus was sailing the ocean blue.
It is performed basically as it has always been done, the only exception being the equipment used to perform the cutting. To simplify, cut rifling involves actually cutting or scraping the grooves in the steel to eventually form the lands and grooves of the rifling.
These days, specialized equipment is used to insert a cutter in the drilled-and-reamed bore of the billet in order to cut and remove a small amount of steel with each pass of the cutter.
While the cutting is going on, either the steel billet or the cutter is slowly rotated to form the twist in the rifling. Such twist normally is specified in number of inches required to complete one full turn in the bore.
For example, the usual twist for a 30-06 is one in ten or 1:10. That means that the rifling requires ten inches to make one complete turn in the bore.
The cutter is passed through the bore as many times as is necessary to cut the grooves to the desired depth, one groove at a time. The number of grooves cut in a barrel is variable, but three, four or six are the most common.
Button Rifling
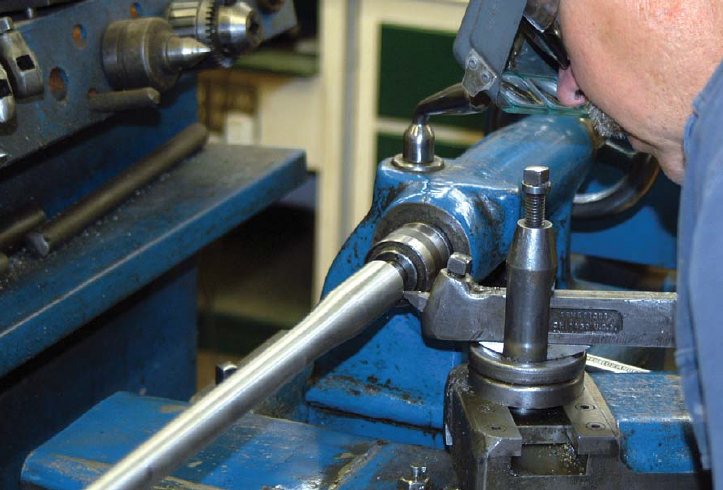
Perhaps the most commonly used method today among custom barrel makers is button-rifling.
In this method, the deep drilling and reaming are the same as for cut-rifling, except that the finished hole is slightly undersized for the button system. The barrel maker either makes or purchases a carbide “button” that contains the rifling impression in reverse in the button.
Once the bore is drilled and reamed, this button is either pushed or pulled through the bore, essentially “ironing” the rifling into the steel of the bore.
Whether pulling or pushing the button is the best method remains the subject of debate with advocates on both sides. I think that it is safe to say that a majority of barrel makers using the button method pull the button through the bore.
Still, some much prefer pushing the button through. Excellent barrels can be and are made using both methods.
Hammer-Forging Rifling
The third method of rifling is hammer-forging.
Another German development, this method is not in common use among custom barrel makers. In fact, I don’t know of a single one that hammer-forges their barrels.
Many factories do, however. The cost of the equipment to hammer-forge a barrel is very expensive and is cost effective only for high volume barrel production.
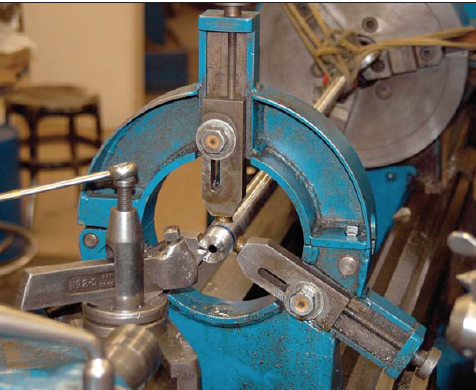
Hammer-forging is quite similar to button-rifling. In hammer-forging, the barrel billet is drilled and reamed as with the other systems. However, the billet is much shorter and much larger in diameter. The billet is inserted on a precisely finished bore-size mandrel containing the rifling (and in some cases, the chamber and outside contour as well) in reverse.
This mandrel, with its stubby barrel billet attached, is then inserted into the hammer machine which literally pounds the steel in the billet to form not only the rifling in the bore, but some machines also forge the outside of the barrel billet to the final contour.
One company, I believe it was Steyr from Austria, proudly proclaimed that their barrels were hammer-forged and the spiral hammer marks were left on the outside surface of the barrel to prove it.
This system is very fast and very efficient at producing barrels in quantity and quality. The best of the hammerforge machines will produce a barrel about every three or four minutes.
The commonly held view is that hammer-forging produces the least desirable quality barrels of the three methods although I haven’t found this to be particularly true. Very high quality barrels can be and are produced using all three of these methods of
production.
Personally, I think the major difference in quality of barrels produced by all three methods is much more dependent on the experience of and care exercised by the operator and the condition of the equipment being used than it is the method employed.
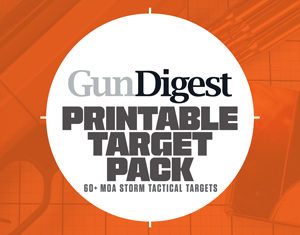
Next Step: Get your FREE Printable Target Pack
Enhance your shooting precision with our 62 MOA Targets, perfect for rifles and handguns. Crafted in collaboration with Storm Tactical for accuracy and versatility.
Subscribe to the Gun Digest email newsletter and get your downloadable target pack sent straight to your inbox. Stay updated with the latest firearms info in the industry.