At GunDigest, we independently review products. However, we may earn a commission when you purchase through links on our site. Learn More
.223 vs 5.56: The Ultimate Comparison & Review
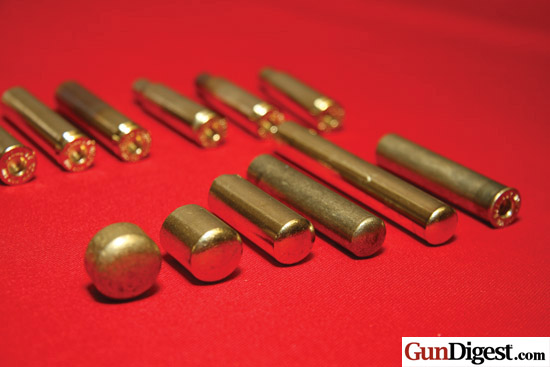
.223 vs 5.56: A History
To a whole lot of shooters, ammo is ammo—if it fits, it shoots. These shooters tend to be the guys with seriously tired, worn, or even busted firearms. They also tend to focus on the wrong thing; you know, the guy who scrubs the brass marks off his ejector lump, at least until one day his rifle stops working or breaks into many pieces.
Ammo is not ammo. And when doing a .223 vs 5.56 comparison, while the loads are almost identical, they are not the same. To know why, we have to go back to the beginning.
The early 1960s were an interesting time. The returning GIs from WWII and Korea had a decade to get things the way they liked. Two tastes they acquired during that time were varmint shooting and benchrest. Varmint shooting was simple. Various members of the rodentia clan, going about their usual business in a field or pasture, served as animate targets. They were prolific breeders, there was no limit, no season, no quitting. You could shoot all day if you wished. Well, as much as shooters then and now like to shoot, shooting varmints with a .30-06 was just silly. The recoil would beat you up, the noise was alarming, barrels got really hot really fast, and the cost of ammo, even back then, was just off the charts.
So they went down in caliber until they found that various rifle cartridges using .224-inch bullets did the job nicely.
Benchrest shooting was a refinement and variant of target shooting. Instead of trying to coax all the shots into a 10-ring, the group was the score. The smaller the group, the better the score. Again, smaller was better, and the common .224-inch diameter bullet served well.
The premier cartridge in the early 1950s, when varminting and benchrest got started and began revving up, was the .222 Remington. Introduced, in 1950, in the Remington 722, it was superbly accurate, and the rifle was also a brilliant out-of-the-box shooter. The mild recoil would not cause a benchrest shooter to have aiming problems, and the mild report, efficient powder charges and low bore erosion made it a useful varmint cartridge.
For those who needed more reach in the varmint fields, Remington came out with the .222 Magnum in 1958, offering 2-300 fps more velocity than the little .222.
Now we shift gears from varminting to the on-going soap opera of the U.S. Army rifle situation. Having spent a decade and millions of taxpayers dollars, the U.S. Army Ordnance bureau has brought forth … an improved M1 Garand. And so screwed up is the process that they can’t even produce rifles quickly enough to arm the U.S. Army in any reasonable time frame. I once looked into the numbers and came to the conclusion that, at the rate the Army was buying and building (the U.S. arsenal at Springfield was still open then), the entire U.S. Army would not have been switched over to the M14 before the bicentennial. For those who don’t remember that occasion, the year was 1976.
So, the Army finds, in the mid-1960s, that the Armalite rifle is one that could actually be forced upon them. They pull out all the stops and do everything they can to prevent this. “Real men shoot .30 rifles” was the prevailing ethos of the day (and in some circles, still is).
The cartridge the Armalite rifle was chambered for was the “.222 Special,” a case halfway between the .22 Rem. and the .222 Rem. Mag. It also split the difference between them in velocity. The Army, recognizing an opportunity, first accepted the velocity as sufficient. Then they upped the stakes and insisted on better and better down-range performance. Basically, they kept asking until they had exceeded the pressure limits of the .222 Special. But the problem is that pressure is not simply velocity-dependant. Still, the designers had managed to meet the velocity specs, and the rifle was adopted.
I have now, in less than 700 words, summarized years of work, 100,000 man-hours of engineering, manufacturing and range testing, and we’ve only begun.
.223 vs 5.56: Measuring Pressure
Before we get too deep into this, you also have to be aware of a change that happened in our lifetimes (well, the lifetimes of the old farts among us), and that is the change in pressure measuring. If you have an older reloading manual, you’ll see the measuring units denoted in C.U.P., and in some older manuals “CUP” and “PSI” are used interchangeably.
The old way of measuring pressure was known as the copper crusher method. In it, a test barrel would have a hole drilled through it to a specified set of dimensions. Then, a little copper cylinder was clamped in place over the hole. When the round was fired, the copper cylinder got hit with the pressure and was compressed. By measuring the length of the cylinder before and after, ballisticians could determine the peak pressure. This was known as “copper units of pressure,” or CUP, but was often expressed in pounds per square inch, or PSI. The copper (and lead cylinders, used for lower-pressure calibers) could only tell us what the peak pressure was, however, not how fast its onset was, how long it lasted, etc.
Today, transducers, or strain gauges, are used to measure pressure. Here, the gauge, which is essentially a transistor (it is more complicated than that, but we’re discussing firearms, not electrical engineering) is fastened to the barrel. When the gauge is stressed, the electrical resistance of the gauge changes. The beauty—and the problem—with this method is that it is dependant on a computer or other recording device. Depending on how much you spend, you can record the pressure of the event hundreds, thousands, or more times per second. This caused problems in published loading data.
Let’s construct our own cartridge, just so we can remain theoretical for the moment. The “.30 Zoomer Magnum” has a maximum average pressure (MAP, or the allowed peak) of 50,000 CUP. We use the newfangled transducer to measure the standard reference load (in this case, 42 grains of “XYZ” powder under a 183-grain soft-point) and come up with 57,000 PSI. The “new” MAP for the .30ZM is now 57,000 PSI, where before it had been 50,000 CUP. But the actual pressure has not changed, we are simply using a new yardstick to measure it with.
Then we run into problems. In checking loading data, we find that some of the data wasn’t as “clean” as we thought. An example: using “123” powder under the same 183-grain soft-point, we had found that we could get 100 fps more and still only see 50,000 CUP pressure. With the new transducer and seeing things in thousandth of a second slices, we see that, yes, the main pressure peak is only 57,000 PSI, the allowed max by the new yardstick, but we also see a second, higher, spike from the bullet hitting and stalling in the rifling. That spike comes in at 63,500 PSI, well over the maximum allowed. So, we have to throttle back the load data, and all of a sudden “123” powder loses its 100 fps advantage.
The problem came from the copper cylinder not being sensitive enough to register the second, over-max pressure spike, so, no, we have not “slowed down the load data to satisfy the lawyers.” We didn’t know we were going over-max before. We do now, and we have to adjust the data. (Oh, and just to add to the confusion, where you place the transducer can also have an effect on the pressure you measure.)
The SAAMI-spec pressure ceiling, the MAP allowed for the .223, is 55,000 PSI. No, there is no handy-dandy formula that lets you convert old copper-crusher pressures to PSI. The ballisticians tried, and they tried really hard, to come up with a conversion factor. The trouble they ran into was that every cartridge seemed to have its own factor. It was bad enough converting from CUP to PSI, but trying to tell people (and this is just an estimate, don’t use these as numbers to go by) that where they could use a plus-12 percent CUP-to-PSI factor for the .293, the .34-06 used a plus-15 percent, and the .305 used a plus-nine percent. (And, yes, I deliberately used nonsense calibers. Don’t try to decipher them, there is no pattern, nor any useful info beyond what I just told you.)
There was no way to formulate an equation for a “universal translator” of CUP to PSI. Give it up, forget the conspiracy theories your gun club buddy tells you, just accept the new info for what it is.
The NATO spec for 5.56 has a higher “ceiling,” but it’s also measured slightly differently, and, again, there is no handy-dandy conversion. The SAAMI method measures pressure at the middle of the case. NATO (the European measuring group is known as C.I.P.) measures at the case mouth. A CIP-spec 5.56X45, measured at the case mouth, shows a pressure of 62,000. Measured at the case middle, as SAAMI does, it shows 60,000 units of pressure.
.223 vs 5.56: Things Get Ugly
But the problem isn’t just pressure. That CIP pressure of 62,000 PSI? It is measured in a 5.56 chamber. If we take the same round, which shows 60,000 PSI/SAAMI (still 5,000 PSI over the .223 max) and put it into a .223 chamber, things get ugly. Really ugly, and really quickly. The pressure spike piles onto an already over-pressure round. I’ve talked to professional ballisticians, guys who use million-dollar labs to measure ammo for their ammo manufacturing bosses. (You know, those guys with the computers and transducers than can measure pressure by the thousandth of a second or finer.) They have reported some instances of 5.56 ammo in .223-chambered pressure barrels demonstrating peak pressures at or above 75,000 PSI. That is the pressure of the proof load each rifle gets tested with at the rifle maker’s, before shipping.
Proof loads, for those who aren’t remembering, are the deliberate, plus-30 percent loads that each rifle maker fires, once per gun, in their rifles before they ship them. They do so in the full expectation that the rifle will do just fine. Once. More is abusive, stupid and asking for trouble.
At this point, many an advocate of “there is no difference” will say “I’ve shot thousands of rounds through my AR and it hasn’t given me any problems.” I’ve worked in gun shops for too many years to accept round-counts mentioned across the counter at face value. Nothing personal guys, but the true number of rounds fired is typically a quarter to a tenth of the asserted number. I teach law enforcement patrol rifle classes in the summer, and I see how much work (and have done it myself) it takes to run 1,000 rounds through a rifle. If your buddy says “Yea, we went to the range this weekend and put a thousand rounds through each rifle,” he’s exaggerating. And if he isn’t, you do not want to borrow any of his rifles, as a thousand rounds in two days is enough to smoke the barrel.
Also, most shooters haven‘t fired enough real 5.56 ammunition to actually test their rifle. Almost all the “generic” ammo you shoot is not 5.56. Oh, it says “.223 Remington/5.56” on it, but it isn’t really 5.56. The high-volume, low-cost bulk ammunition that most of us use is not loaded right to the red line. I’ve chrono’d enough of it to know that much of it falls 100 to 200 fps short of full-book 5.56 spec. That right there is enough to make it no big deal chamber pressure-wise, because the peak pressure of the .223 load is sufficiently less than that of the 5.56 that the artificially-induced spike still falls below the pressure ceiling.
The extra pressure produces faster wear on your rifle. Since most shooters don’t shoot enough to wear out their rifles in any reasonable time frame, the extra wear is hardly noticed. But you can have a serious problem if the variables stack up against you in a range session. Rifles get hot when you shoot them. They also get hot in the summer, in the heat and the sun.
So there you are on a hot summer day, shooting your supply of real-deal 5.56-spec ammo through your .223-chambered rifle. The summer sun beats down and pressures rise. Black rifles left in the sun can easily reach 140 degrees even before they’re fired. Add to that the temperature increases from shooting, and you have some real heat problems coming on. Let’s make it worse: the particular lot of your 5.56 ammo is at the top of the allowed pressure and at the bottom of the allowed brass hardness. The ammo maker tested it in a 5.56-chambered test barrel and, while it was in the top end of the allowed specs, it is within the safety margin.
You’re having a blast, when all of a sudden your rifle stops working. What happened? Well, the heat increased the already maximum-made-excessive pressure and, on extracting a fired case, the pressure had expanded the case enough for a primer to fall out of the primer pocket and into your rifle. Actually, it probably has been losing primers for the last couple of magazines—pick up and inspect all your brass. You’ll see you’ve been losing ne or two primers per magazine. But it wasn’t until one fell into your action and tied things up that you noticed.
How bad can this get? In a patrol rifle class last year, a police officer was pushing his safety back to Safe (and the selector was resisting), when the rifle suddenly spat out a three-shot burst, then stopped working entirely. He’d blown a primer, and the anvil of the primer had wedged under the trigger in just such a way as to create the burst. Typically, the primer wedges under the trigger in such a way as to keep the rifle from shooting at all. Either way, not good.
.223 vs 5.56: Solving the Problem
One solution would be to only use .223-spec ammo. That can be okay, but, if you find a deal on 5.56 ammo, it kind of makes no sense to buy a “deal” you can’t use. Also, some of the best ammo for some applications is 5.56-only. Plus, you can’t control the outside temperature and probably not how much ammo you may need to fire. It would be nice to have a rifle that handled 5.56 with aplomb. But how? To begin with, you have to be able to measure what is there.
The first thing you have to know is this isn’t about headspace. A headspace gauge only tells you the dimensions of the shoulder and case body, not the neck and leade. You need a leade/throat gauge, and for that you need to get a .223/5.56? Gage (yes, the “?” and misspelled “Gage” are the part of the correctly named product), from Michiguns (www.m-guns.com). I have to be up front and tell you that I have known Ned, the inventor, for nearly 30 years. I don’t get anything but thanks from him for recommending his great gizmo, and I think it is useful enough that I’d recommend it if I didn’t know or even like him.
The Gage is simple and ground to just under the maximum specs of a 5.56 leade/throat. Drop it in and, if it drops free, you have a 5.56 leade. If it sticks (it is hardened steel, don’t pound it in), you have a .223 leade. If you’re curious and want to know just where exactly it is catching, you can mark it up with a felt-tip pen and, with a little careful turning (clockwise), you can see where it rubs. If you are really curious, browse through your Brownells catalog—you do have a Brownells catalog, don’t you? You don’t? Get one, before you get severe deductions from your man-card—and order Cerrosafe. Cerrosafe is a special metal alloy with a low melting point. You push a cleaning patch until it is in front of your chamber, heat the Cerrosafe, pour it in the chamber and let it cool. Once cool, you push it out of the chamber, and now you have a cast of the chamber, throat, and leade. You can inspect and measure to your heart’s content.
So, with the Gage or Cerrosafe you find that you have a .223 chamber and you wanted a 5.56. If the rifle is still brand-new, you can send it back. However, the maker probably only has more barrels of the same kind from the same maker, and you may not get a 5.56 no matter how many times you ask. So, you need a specialized reamer. One that cuts the leade and the leade only. (You don’t want your headspace changed.) Ned makes that, also. Now, I can hear some of you saying, “But, I have a chromed barrel, I don’t want to cut the chrome!” Okay, stick with a chromed .223, that’s fine.
But, if you want a 5.56 leade, yes, the reamer will remove chrome. But guess what? The area being cut is the area where the chrome is blasted off first, so if you’ve put more than a few hundred rounds down your barrel, there’s probably not much chrome left there anyway, especially if you did rapid-fire shooting or heated the barrel up to the point where you had to wait for it to cool.
In all fairness, you don’t have to have Ned’s reamer. Other various reamer makers will be happy to supply you with a 5.56-spec finish reamer. You just have to be aware that a finish reamer will also ream the shoulder, if you aren’t careful. So, you may go in attempting solely to make a 5.56 throat and end up creating excessive headspace along the way. Ned’s reamer does not cut on the chamber shoulder at all, therefore, when you feel it stop cutting, you are safely done. It also makes a leade longer even than that of 5.56, though by a small margin.
What’s that, another protest? “But my barrel is marked 5.56, I can’t have a problem.” Alas, that is not the case.
At my latest LEO patrol rifle class, I chamber-gauged the two dozen rifles the officers had brought. All but two were marked “5.56.” One of those was an M16A1 and the other had a completely unmarked barrel. Of the 24 rifles, six failed the .223/5.56? Gage test. Two of those were not just .223-chambered, but clearly on the small side of the dimensions, as I had to use force to remove the Gage.
How can this be? Remember how barrels are made. The manufacturer uses a chambering reamer to turn the chamber out of the back and of the barrel blank. As reamers dull, they are re-sharpened. Each sharpening makes them fractionally smaller. Reamers start at the maximum size and, as they “shrink” from repeated sharpening, the chamber they cut also changes. Once they get to the minimum, they are discarded and a new reamer is employed. Well, some use reamers for a bit too long, and the chamber cut can be at minimum or smaller dimension.
Of those six that failed the Gage, three ended up showing pressure signs later in the class, so we reamed them with the Michiguns reamer and those problems went away. Two of them were the markedly undersized barrels. The other barrels/rifles continued to work, but for how long? They may have been getting fed .223-pressure ammunition, and thus would not show pressure signs.
Having a .223 chamber in your AR is a greater concern than just the social ostracism of having a rifle that is “not Mil-Spec.” However, it is something you can test and fix, if needed. Me, I’ve long-since checked all my rifles, and those that didn’t pass the test have been corrected.
Next Step: Get your FREE Printable Target Pack
Enhance your shooting precision with our 62 MOA Targets, perfect for rifles and handguns. Crafted in collaboration with Storm Tactical for accuracy and versatility.
Subscribe to the Gun Digest email newsletter and get your downloadable target pack sent straight to your inbox. Stay updated with the latest firearms info in the industry.