At GunDigest, we independently review products. However, we may earn a commission when you purchase through links on our site. Learn More
Built Glock Tough
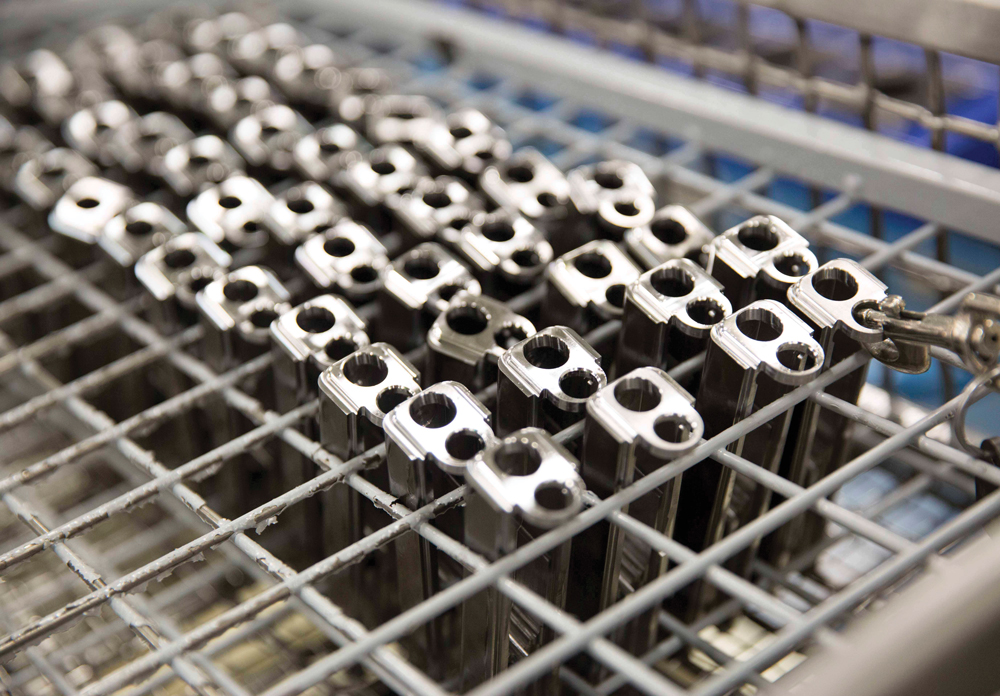
We went behind the scenes at Glock’s new Smyrna, Ga., plant to see how one of the world’s most dependable handgun manufacturers gets it done.
That sums up the challenge for the employees at Glock. Replicating the exact processes from Austria in the company’s Smyrna, Ga., manufacturing plant would seem like a daunting task, but the vision, philosophies and expectations of Gaston Glock himself drive success at a somewhat mind-numbing level of detail that has to be seen in order to be believed. The end result, regardless of what the Internet “experts” say about the differences between Austrian- and U.S.-made, is that a G19 is a G19. Period.
This past March, I joined several other media members for an exclusive first look inside the manufacturing operations at Glock’s Smyrna plant. This was a “golden ticket” visit for sure, and it was exciting to be one of the first outsiders to get a chance to understand what makes a Glock a Glock. The visit tied in with the top secret introduction of the new single-stack 9mm G43, and our group of six was among the first from the public to enjoy the chance to send lead downrange with the compact model.
Inside the factory, Dr. Michael Jacquorie, senior executive vice president, walked us through the plant’s major manufacturing processes. For the barrels and slides, there is tool pre-setting, milling, forging and turning, and surface treating, while a polymer process accounts for the frames and boxes.
Glock has insulated itself from material shortages and quality issues by “insourcing rather than outsourcing,” Jacquorie explained. Pointing to a rack of tools with labels such as “milling cutter,” “end mill,” “slot mill” and dozens of others, he emphasized that Glock “makes all of our own tools in Austria. We have no reliance on outside vendors. It guarantees quality, a perfect match every time.”
Glock further guards against supply chain interruptions by using two vendors for its steel and two more for its polymer supply.
“We are market-driven, not shareholder-driven,” Glock’s Jacquorie emphasized. “We keep six to nine months of stock on hand. That’s on top of our regular forecast.”
While the details of our tour were an exercise in sensory overload as Jacquorie whisked us from one machine to the next, the biggest takeaway was that so much of Glock-Austria and Glock-U.S. is interchangeable. From the layout of the machines on the factory floor to the duties of the workers, the process is designed so that an Austrian could come to the U.S., or vice versa, and be up and running at his specific task immediately.
Simple Genius of Glock
“In the operational side of the house, there are two major reasons why Glock is so successful,” Dorsey said. “One is the simplistic design with 34 parts. That’s versus the 200-some parts in a 1911. The more parts you have the more parts can go wrong.
“The second part of the genius is the control of the mass production of the product. The chain of custody of the parts is very transparent, and people are held accountable up and down the chain for the work they do. That control is the secret to how we can mass produce with a high degree of certainty and can replicate the part, which gives us the interchangeability between the guns.”
Everything that happens inside the walls of any Glock production location is driven by what Dorsey refers to as the company’s ethos, or character.
“Mr. Glock’s challenge to us each and every day is to personify perfection,” Dorsey said. “Our focus is on those who go in harm’s way. We understand the seriousness of what it is we do here and why the products we produce need to be used, and how important it is for those who go in harm’s way that the firearm, regardless of what environment you’re in, will function when it’s time to use it.”
“Your ability to react, to succeed and to survive in a bad situation basically comes down to one word: confidence. Confidence in yourself. Confidence in each other. Confidence in your training. Confidence in your equipment.”
Along every step of the manufacturing process, 20 percent of personnel are solely dedicated to quality assurance. Further, each new model endures 40,000 rounds of punishment before it goes into production.
“We’ve got the reliability part down,” Dorsey said as the tour wound to an end. “That’s what drives the confidence. If we stay focused on those things while maintaining our ability to evolve with the market, Glock will continue to be successful.”
This article appeared in the May 2015 issue of Gun Digest the Magazine.
Next Step: Get your FREE Printable Target Pack
Enhance your shooting precision with our 62 MOA Targets, perfect for rifles and handguns. Crafted in collaboration with Storm Tactical for accuracy and versatility.
Subscribe to the Gun Digest email newsletter and get your downloadable target pack sent straight to your inbox. Stay updated with the latest firearms info in the industry.